The control of corrosion and erosion damages is one of the essential engineering tasks solving of which ensures the long performance of the objects and constructions. Moreover, despite all the measures taken to increase the corrosion resistance of materials, control and monitoring of appearance and development of corrosion and erosion damages remains one of the most important elements of the Risk Based Engineering. These tasks are relevant for almost all major industries: nuclear, thermal and hydropower, chemical and petrochemical industries, oil and gas, piping, naval, railway and automotive transport, and others.
Corrosion NDT and monitoring – application of the Sonocon B/BL and ExScan1000 instruments
From this article you will learn:
-
The branches of industry where corrosion and erosion monitoring is applicable.
-
What the kinds of corrosion are.
-
What the NDT means for corrosion and erosion detection are.
-
The types of ultrasonic devices for corrosion and erosion monitoring.
-
OKOndt Group company’s products for corrosion testing advantages.
Introduction
The control of corrosion and erosion damages is one of the essential engineering tasks solving of which ensures the long performance of the objects and constructions. Moreover, despite all the measures taken to increase the corrosion resistance of materials, control and monitoring of appearance and development of corrosion and erosion damages remains one of the most important elements of the Risk Based Engineering. These tasks are relevant for almost all major industries: nuclear, thermal and hydropower, chemical and petrochemical industries, oil and gas, piping, naval, railway and automotive transport, and others.
It is worth noting that, besides a wide range of objects and enterprises, there is a plenty of corrosion and erosion types, which are subject to detection: pitting and pilling corrosion, general thinning, erosion, weld joints and HAZ corrosion, and others.
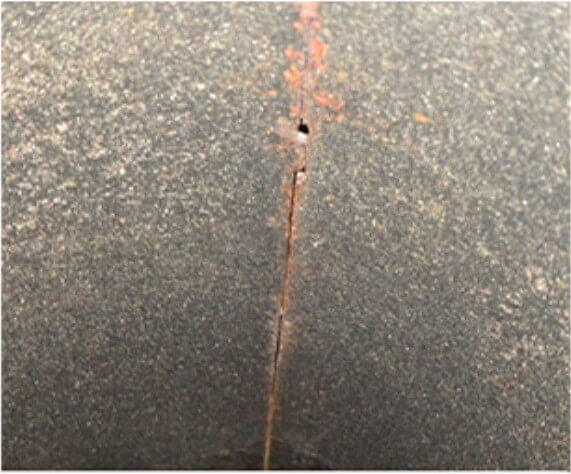
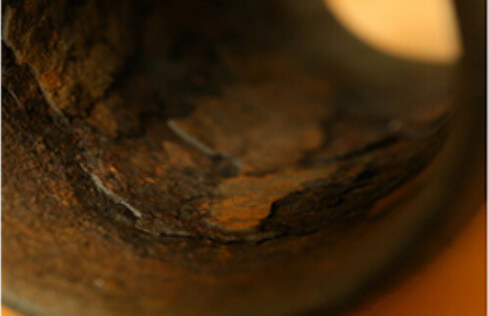
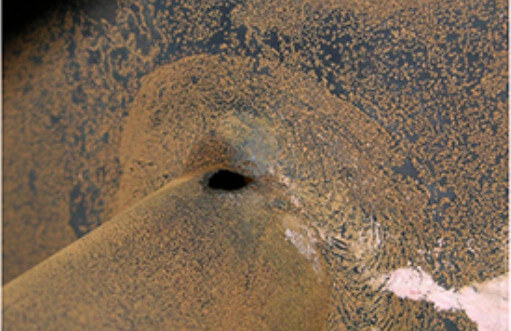
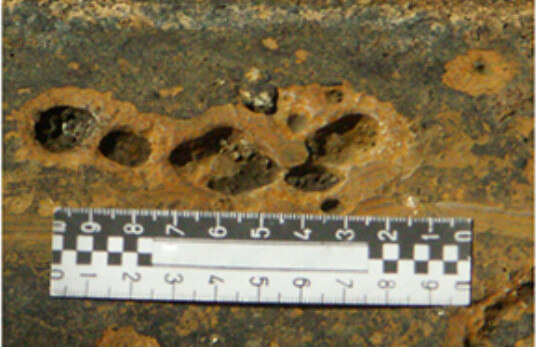
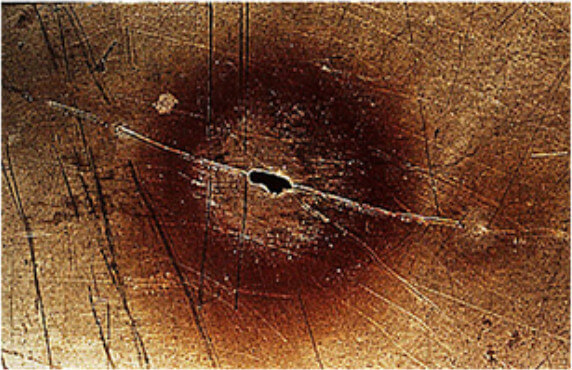
In order to solve each of these tasks, our company offers a range of relevant corrosion measurement NDT equipment.
ExScan1000
For easy tasks not requiring structural data storage or corrosion mapping, a simple, reliable and easy to use ultrasonic corrosion gauge ExScan1000 is used.
The device operation is maximum simplified. You have to connect the transducer, to calibrate the device on the in-built calibration block – and you may start measurements. The device also supports one-point and two-point calibrations.
When taking measurements there is also a so-called gauging accuracy indicator displayed on the screen – the more it is filled, the more accurate measurements are.
A standard gauge mode is used to identify general thinning caused by corrosion or erosion damages. Still, to find a trouble spot of the pitting and pilling corrosion, there is a scanning mode in the thickness gauge. In this mode, the frequency of measurements is increased, as well as a minimum thickness reading is recorded for the current scan session.
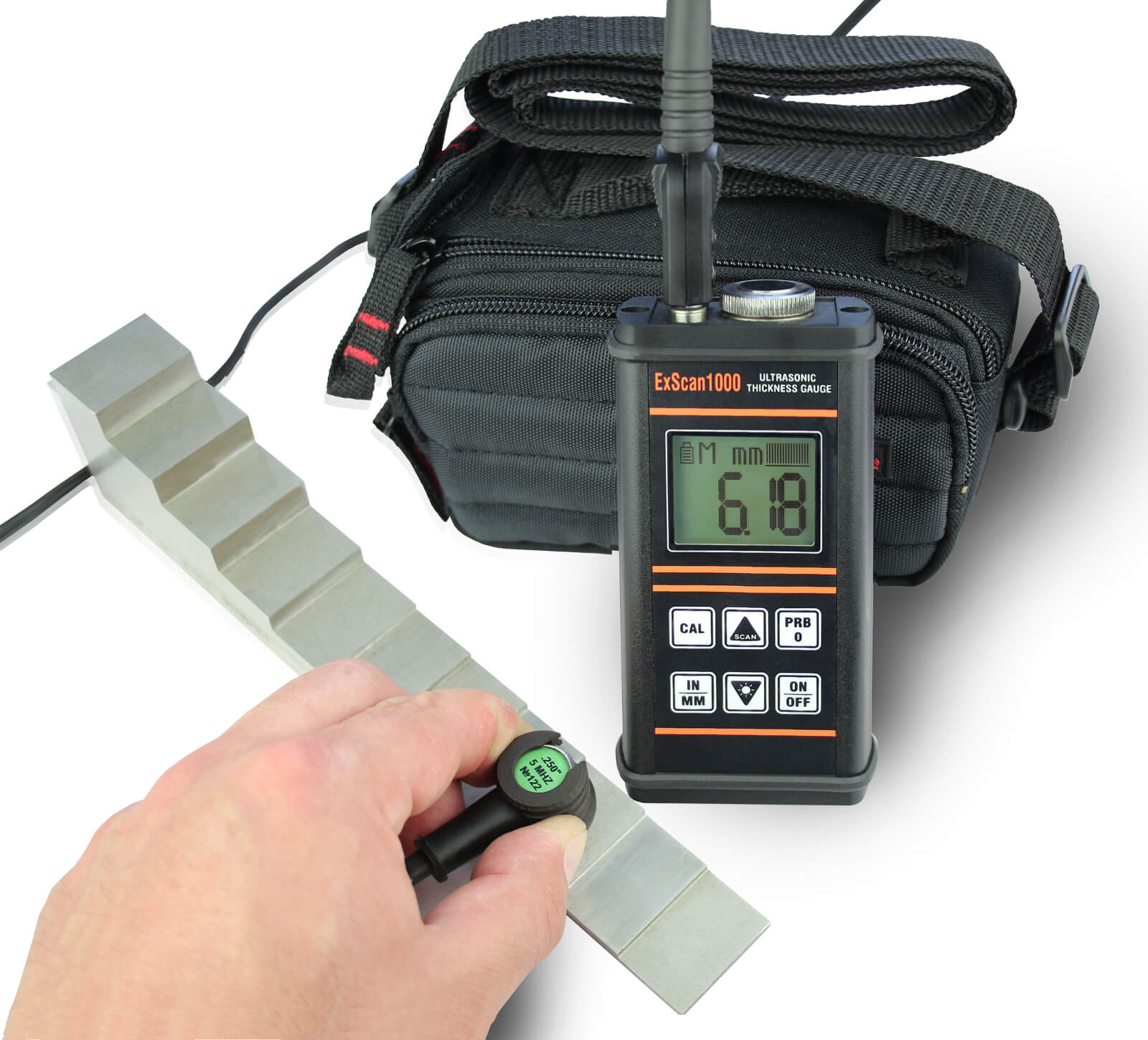
Sonocon B/BL
There is also a wide range of tasks, where it is required not only to measure the remaining thickness and search for corrosion damages, but also to analyze the whole measurements picture, their statistical analysis, measurements database and test reports formation. In order to solve these tasks, there are the Sonocon devices family made by OKOndt Group: Sonocon B and Sonocon BL. The devices have the same set of functions differing only by their form-factor. Sonocon B can be easily fit in your hand and weighs only 2 lb, though it is equipped with 800×480 pixels and 4.5 in display. Sonocon BL has 7.5 in diagonal screen with the same resolution, polyurethane-reinforced bumper case and extended keyboard. Meanwhile, its weight is only 3.5 lb.
Both devices have switchable software allowing to apply them as a universal flaw detectors («UT» version), and as the A-Scan ultrasonic corrosion gauges, and corrosion plotters («Thickness gauge +» version). With regards to the subject of the article, further we will speak about «Thickness gauge +» version functionality.
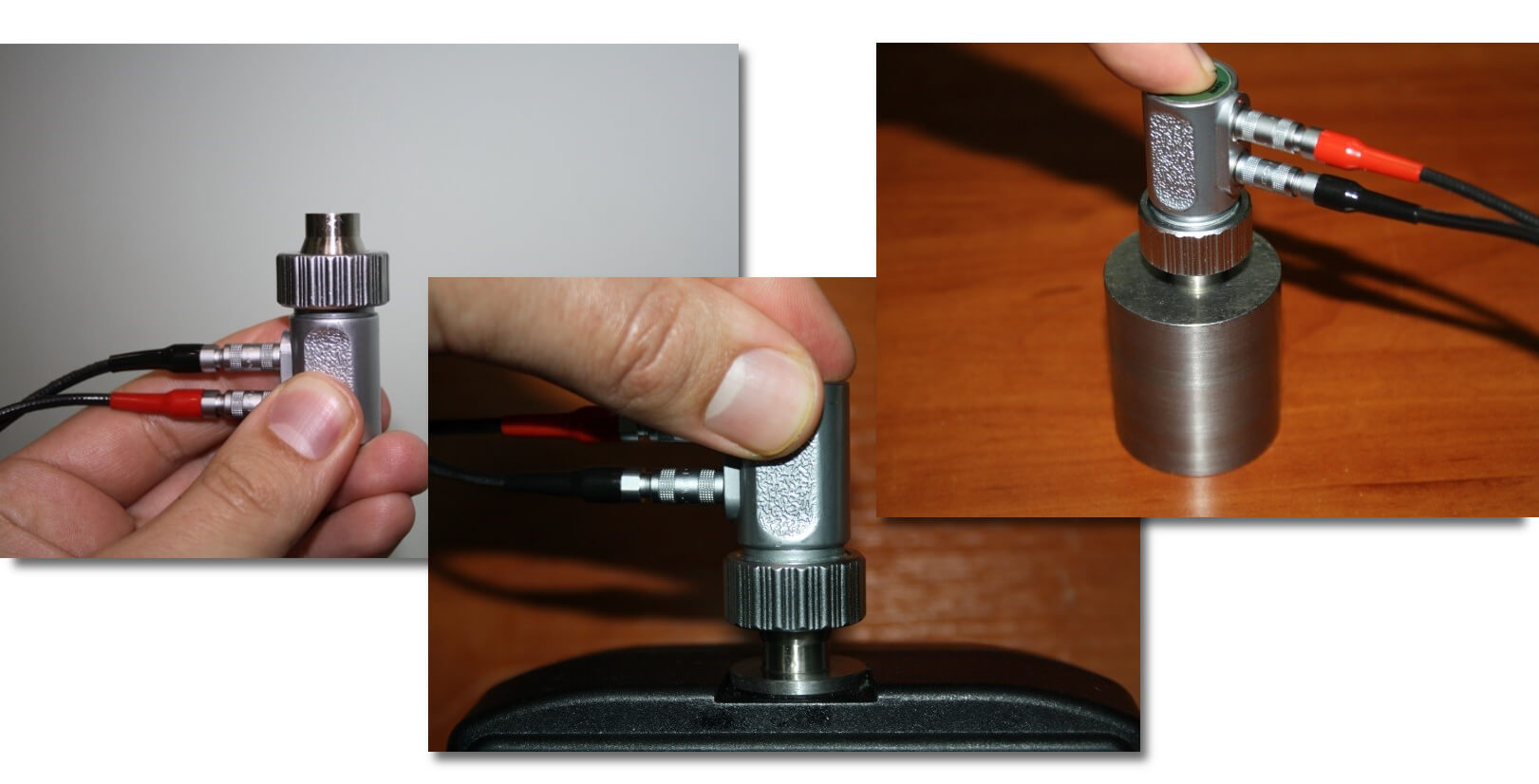
-
Easy to use
Taking into account that the majority of thickness gauging specialists got used to operate simple devices which do not require any complex setup, our developers did their best to automate all procedures necessary to prepare the device for operation as much as possible. For instance, instead of configuring the parameters of an applicable probe, it’s enough to select it from the list – and all the settings will be automatically uploaded. Besides, the device supports a range of automatic calibration procedures: one- and two-point, on the in-built thickness calibration block and even just in the air – without any calibration block!
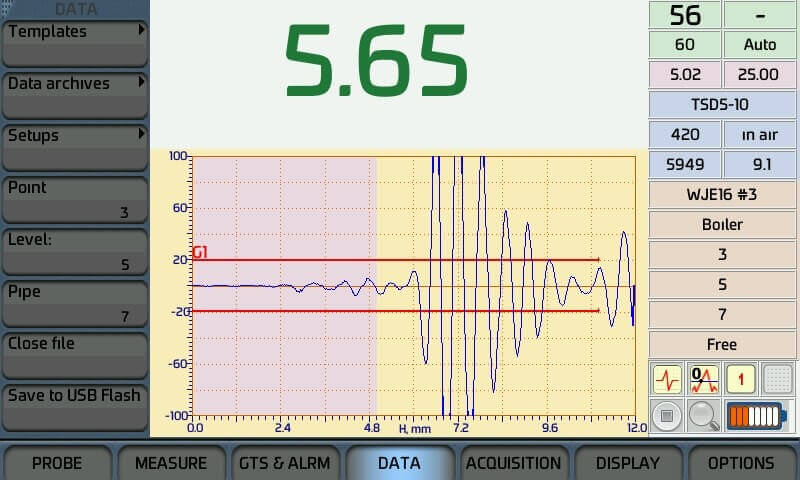
The interface of the device is maximum compact and intuitive: large value of the measurement is green if it is within the acceptable limits, and it is red if beyond them. А-Scan has the visual thickness tolerance marking; the menu and status bar where the device main settings are displayed, as well as the current data file and the location within it, and selected working modes indicators.
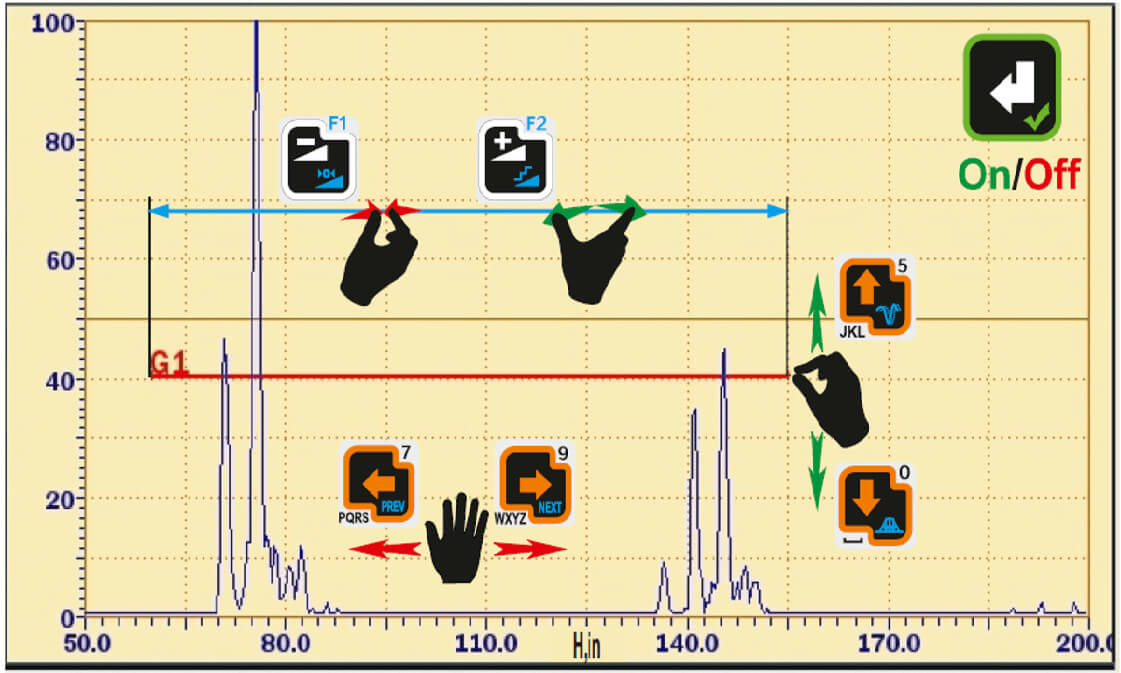
Main parameters control – scan, gate, and the gauge parameters – is performed from the keyboard by pressing just a couple of buttons. For example, upon pressing the Gate 1 button (or the Gate 2), an operator can move the Gate with the buttons ←/→ and ↑/↓, maximize and minimize it with the buttons –/+. It is similar with the rest of the main device parameters.
-
Increasing the measurement accuracy
The measurement process is also automated due to the smart AGC use, which automatically select such a gain (AGC – Automatic Gain Control), that the measurement will be carried out according to the first negative halfwave of the back wall echo-signal.
Moreover, in order to increase the measurements accuracy, not a crossing point of some threshold level is used (for instance, the Gate), but a 0-crossing – whose position does not depend on the signal amplitude.
In cases where it is necessary to perform testing of either high-temperature or, on the contrary, low-temperature objects, a system of temperature compensation of the sound velocity variability is available in the device – to increase the measurements accuracy.
In order to measure small thicknesses, usually the dual-element transducers are used. They allow to detect even tiny corrosion damages at moderate depths. However, they have a significant inconvenience – a beam path from the transmitter to the reflection point and back to the receiver – is not a straight line, but a letter «V», so the time of the back wall echo propagation, especially at small thicknesses, is much more than it would require to go through the object’s thickness and back. This could result in a significant errors of measurement. To avoid this, in all our devices a system of compensation of this error is available – so-called V-path correction, optimized for every dual-element transducer type which is used.
-
Structurising of measurement results
One of the major issues which the inspection companies face when they carry out corrosion monitoring at the large or multiple sites, is the thickness gauging arrangement and the results analysis.
In order to essentially resolve this issue, OKOndt Group put in the Sonocon devices family a template collection for different types of objects:
-
linear – for instance, a small diameter pipe
-
planar – a shipboard, bridge parts, large diameter pipe, vessels and tanks
-
linear set of linear objects – a small diameter pipes range
-
planar set of linear objects – for example, tubeplate
-
linear set of the planar objects – for example, a range of small vessels
-
boilers.
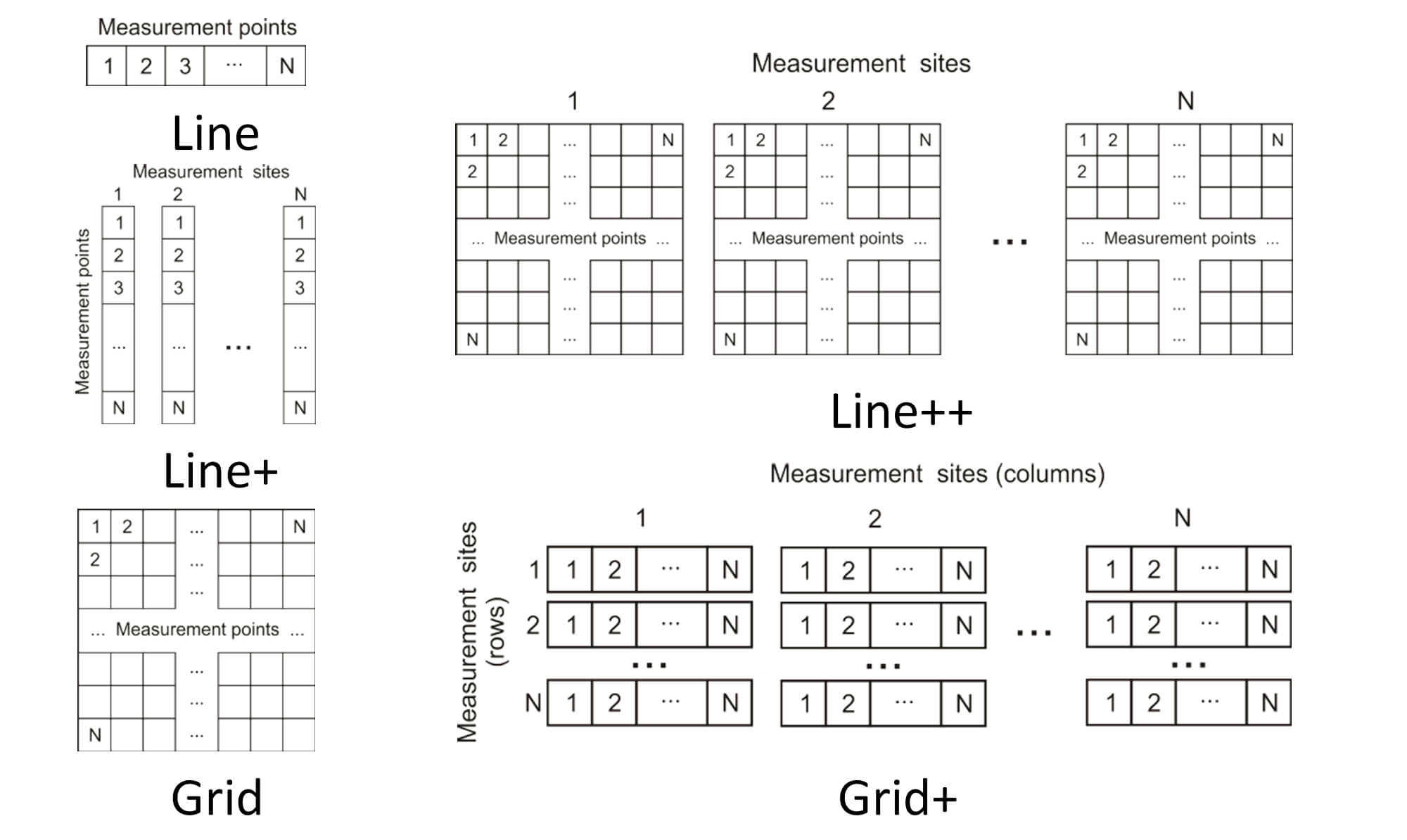
After creation of a data file according to a relevant template, the readings are automatically stored to the appropriate cells of the data file during the testing. There is a possibility to attach comments, A-Scans, B-Scans, C-Scans, as well as micro grids to the measurement sites and points; to mark the sites and points as non-available ones.
Upon completion, and even in the process of testing, there is apossibility to review the main statistical data of every test object.
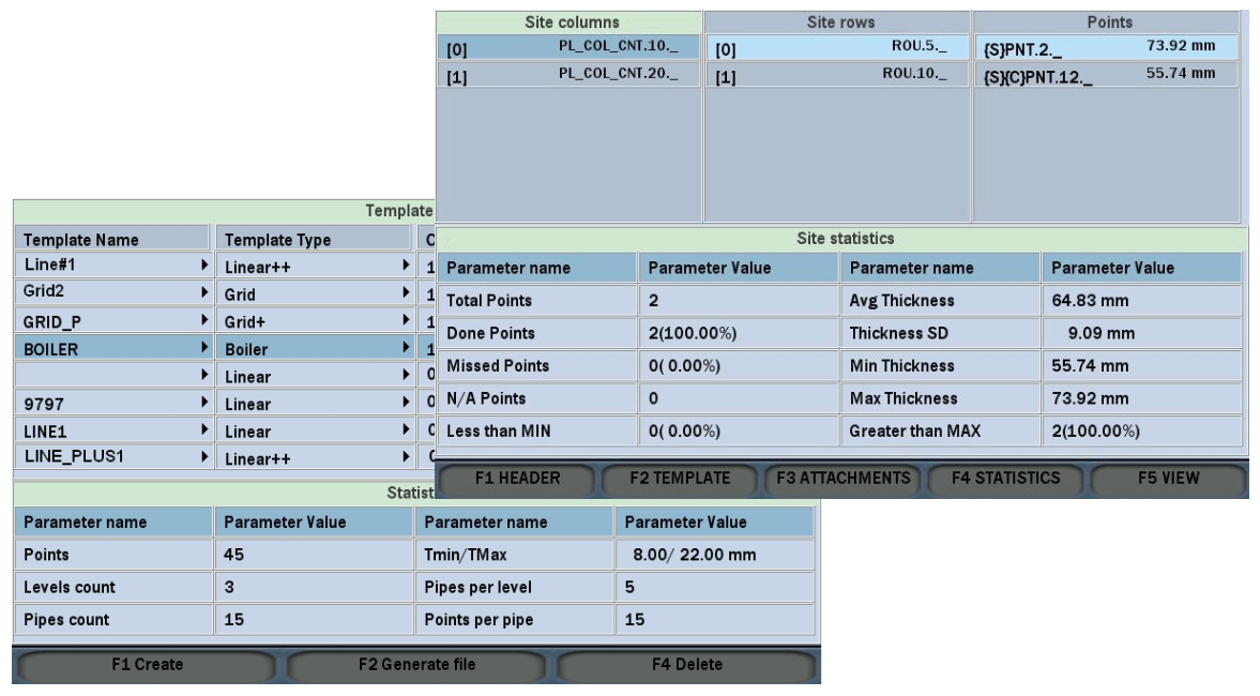
More detailed statistical analysis, as well as test reports creation can be done in the software for the PC which is supplied together with the device.
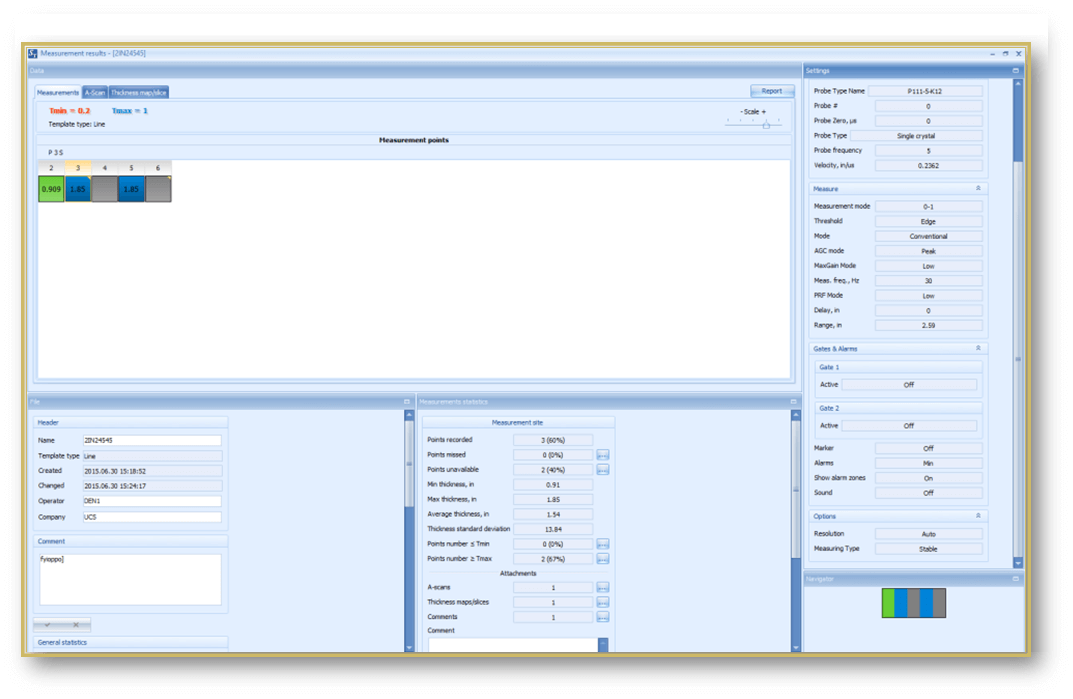
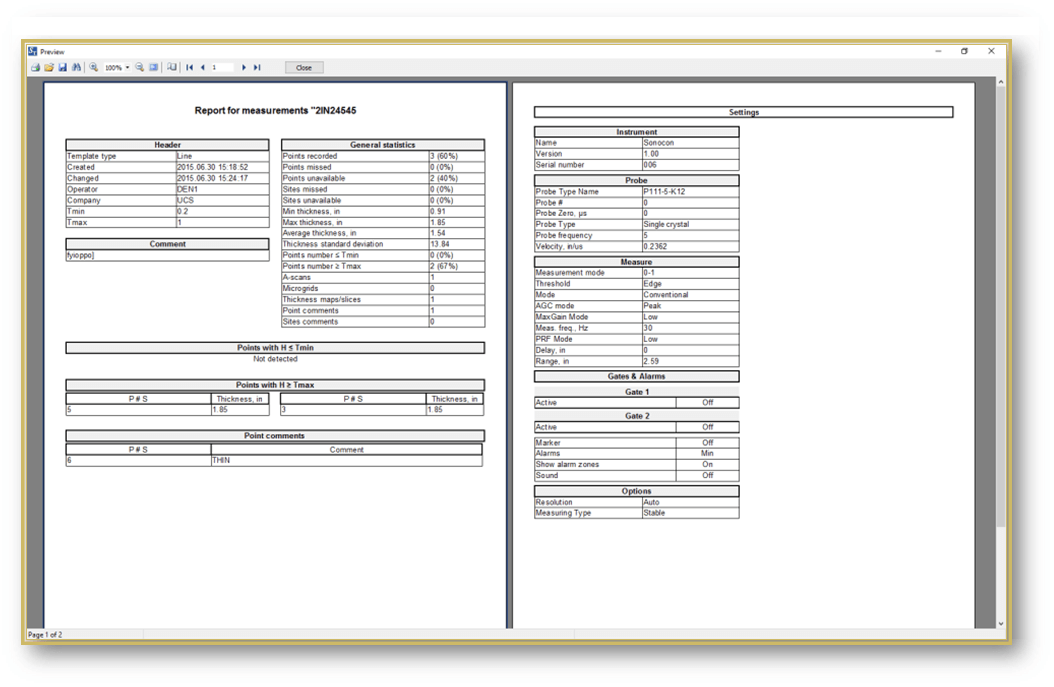
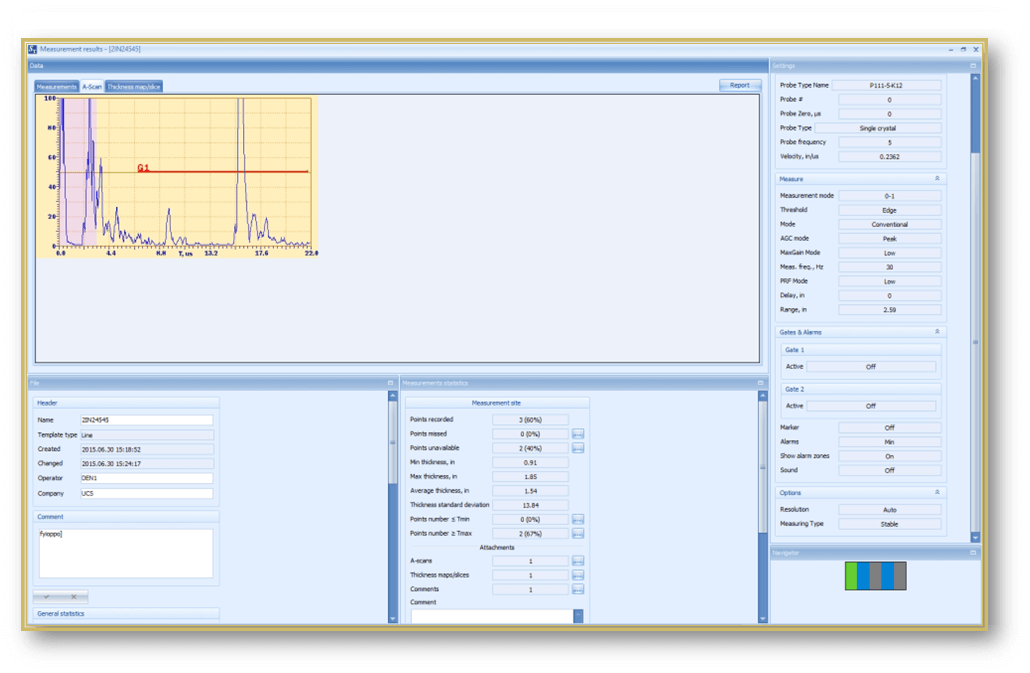
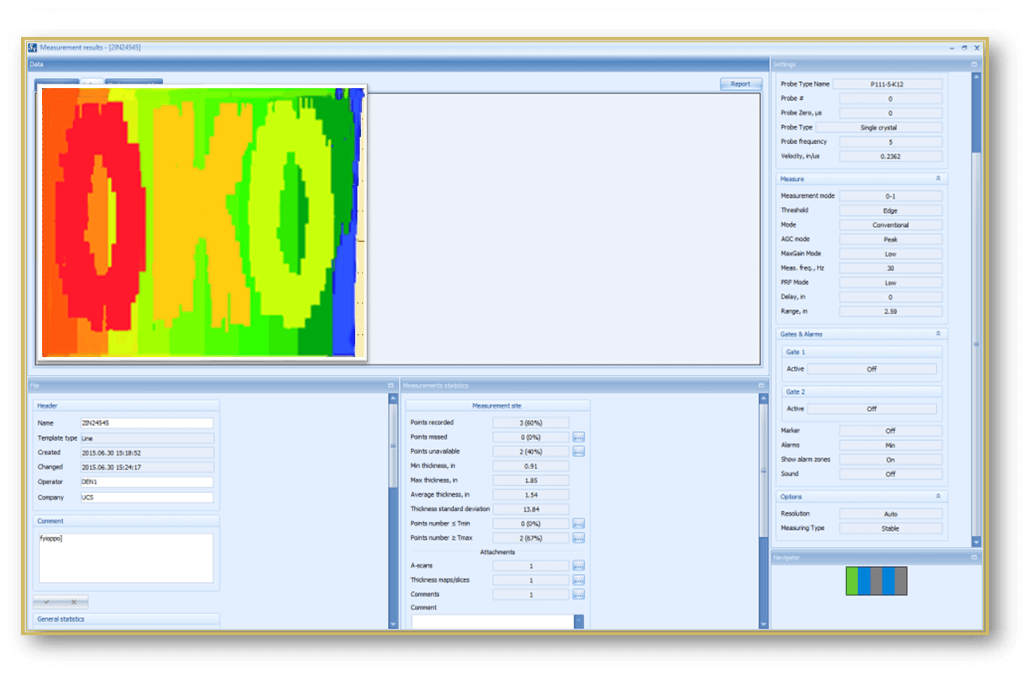
-
Corrosion mapping
The most advanced and illustrative, but at the same time the most expensive and time-consuming way of corrosion damages monitoring is UT corrosion mapping. They distinguish a thickness B-Scans building – thickness cross-sections, and a thickness C-Scans building – the thickness maps. For B-Scans they use single-coordinate scanners, and for C-Scans – 2-coordinates scanners are used.
The thickness B-Scan represents a diagram of dependence of the thickness from the scanning path coordinate, and visually resembles a planimetric cross-section of the test object by the beam of transducer. In the Sonocon family devices this diagram is colored in accordance with the preset threshold values of thicknesses and selected color scheme. So, it becomes immediately clear which parts of the cross-section belong to the defective area. There is a possibility to conduct measurements and to generate reports according to the saved thicknesses cross-sections.
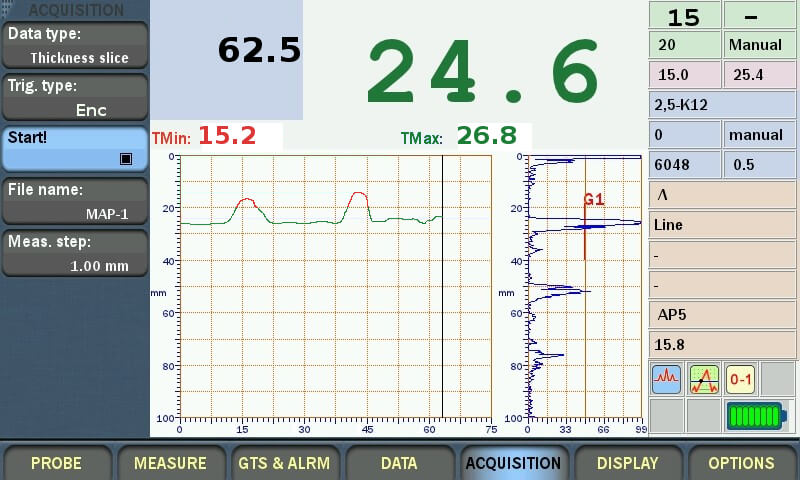
The corrosion map (thickness C-Scan) represents a two-dimensional picture – horizontal projection of the scanned area where the object’s thicknesses are shown in a specific color in every point. What is more, a color scheme is selected in such a way that to visualize thickness deviations from the norm. The corrosion trouble spots in the C-Scan look like hot color spots. Conducting measurements and generating reports according to the saved C-Scans feature is also available.
In whole, the developments and products made by OKOndt Group company are aimed to make metal corrosion and erosion monitoring and measurement processes easier, more comfortable for users, and available from the technical point of view. Moreover, the pricing policy of our company will be a welcome surprise for you.