Las juntas soldadas son el tipo más común de las uniones inseparables en todos los sectores de la producción industrial. Hay una gran cantidad de sus tipos, tanto en términos de métodos de ejecución (por arco eléctrico manual, automático y semiautomático, por arco sumergido, arco en gas de protección, de contacto, etc.), como por tipos de juntas (junta a tope, angular, junta en T, junta de solapa). Sin embargo, no importa a través de qué método se hizo la junta soldada, después de terminar los trabajos de soldadura, en la mayoría de los casos, la junta soldada se inspecciona. La detección de fallas tiene como objetivo la detección de varios defectos que conducen a un debilitamiento de la resistencia y la confiabilidad de la junta, así como a una violación de su hermeticidad. La detección oportuna de tales defectos afecta significativamente la determinación del recurso de explotación de la construcción soldada en general. La calidad de ejecución de las juntas soldadas es especialmente crítica durante la operación de los sistemas y recipientes que operan bajo alta presión, elementos de estructuras sustentadoras.
Ensayo no destructivo de las juntas soldadas
Inspección visual
Inspección por líquidos penetrantes
Inspección ultrasónica
Método de eco e impulsos
Método de eco y de espejo
Método de espejo-sombra
Método TOFD
Inspección de corrientes Eddy
Inspección por partículas magnéticas
Inspección radiográfica
Las juntas soldadas son el tipo más común de las uniones inseparables en todos los sectores de la producción industrial. Hay una gran cantidad de sus tipos, tanto en términos de métodos de ejecución (por arco eléctrico manual, automático y semiautomático, por arco sumergido, arco en gas de protección, de contacto, etc.), como por tipos de juntas (junta a tope, angular, junta en T, junta de solapa). Sin embargo, no importa a través de qué método se hizo la junta soldada, después de terminar los trabajos de soldadura, en la mayoría de los casos, la junta soldada se inspecciona. La detección de fallas tiene como objetivo la detección de varios defectos que conducen a un debilitamiento de la resistencia y la confiabilidad de la junta, así como a una violación de su hermeticidad. La detección oportuna de tales defectos afecta significativamente la determinación del recurso de explotación de la construcción soldada en general. La calidad de ejecución de las juntas soldadas es especialmente crítica durante la operación de los sistemas y recipientes que operan bajo alta presión, elementos de estructuras sustentadoras.
El ensayo no destructivo (NDT) es el método principal para controlar las juntas soldadas, ya que permite mantener la integridad del bloque controlado y su comportamiento funcional. Existen muchos métodos del ensayo no destructivo y una enorme cantidad de modelos de equipos basados en un método particular. Al elegir un método de inspección, es necesario tener en cuenta numerosos factores, tales como el material de las piezas a soldar, la construcción de la junta soldada, el estado de la superficie, los requisitos de calidad, el acceso, el tipo y la ubicación de un posible defecto (discontinuidad), el costo y el rendimiento de la inspección. A causa de esto, no existe un método universal de inspección, y la calidad, fiabilidad y durabilidad del producto final dependerá en gran medida de la elección de la variante más óptima.
Inspección visual
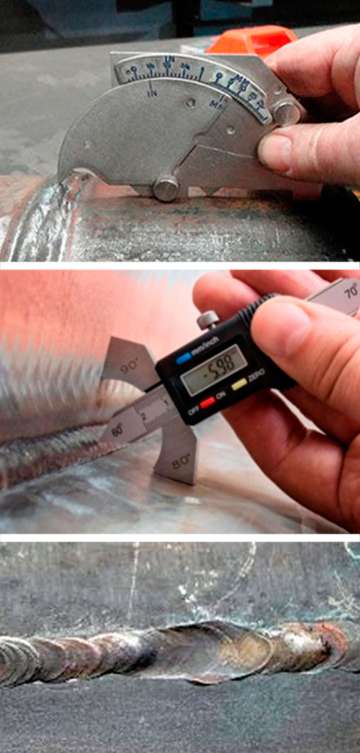
Este método combina la inspección visual y la medición de los parámetros geométricos de una junta soldada controlada para verificar el cumplimiento de los requerimientos.
La detección de fallas debe ser precedida por la limpieza de las juntas soldadas de la capa de oxidación, salpicaduras de metal y escoria. Después de eso, la superficie se trata con alcohol o se desincrusta con una solución de ácido nítrico al 10%.
Como instrumentos para este tipo de inspección, generalmente se usa una lupa con un aumento de 5 o 10 veces, dispositivos de iluminación, así como los instrumentos de medición (regla, compás de vara, plantillas), con la ayuda de los cuales se controlan tanto las dimensiones de la junta como las dimensiones de los defectos detectados.
A pesar de la aparente simplicidad, este tipo de inspección es muy efectivo y precede a otros métodos de inspección. Con todo eso, si se detectan defectos en esta etapa, la junta se considera defectuosa y los tipos de inspección posteriores ya no se realizan. La imperfección obvia de este método es la imposibilidad de detectar la mayoría de los defectos ocultos y la subjetividad de los métodos de evaluación, lo que requiere la existencia de una gran experiencia del especialista que ejerce el control.
Inspección por líquidos penetrantes
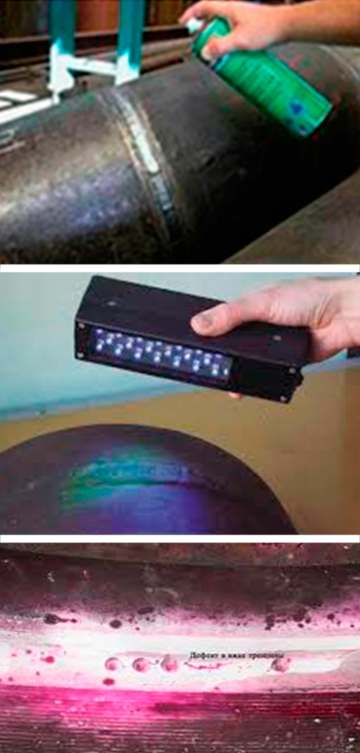
Este método se basa en la capacidad de un líquido de penetrar en los canales más pequeños y llenarlos de sí mismo. En esencia, estos pequeños defectos de la junta soldada son capilares. Por ejemplo, estos incluyen poros y grietas que están contenidas en la superficie del material. La velocidad y la profundidad de la penetración del líquido dependen del radio del capilar y de la humectabilidad del líquido. Por lo tanto, el método capilar es muy efectivo para detectar defectos superficiales.
Para aumentar su eficacia, se utilizan así llamados penetrantes, que tienen una tensión superficial pequeña, y pueden penetrar en la profundidad del capilar. Su color brillante los hace notables, lo que facilita la detección de un defecto. El juego para la inspección por líquidos penetrantes generalmente incluye: penetrante; un limpiador, que es necesario para una limpieza profunda de la superficie antes de realizar la inspección; un revelador, como resultado de aplicación del cual el penetrante se elimina del defecto y crea un dibujo indicador contra un fondo contrastante, según el cual se puede juzgar visualmente las dimensiones y la forma del defecto.
Este tipo de inspección es cercano en su metodología al visual, ya que se realiza mediante la inspección de la junta soldada, por lo tanto, tiene las mismas imperfecciones.
Inspección ultrasónica
La inspección ultrasónica es uno de los tipos de inspección más comunes, ya que permite detectar con gran precisión los defectos ocultos ubicados dentro de la junta soldada. El método se basa en el uso de las ondas ultrasónicas que pasan a través de una capa de metal y se reflejan desde su límite y los límites de las discontinuidades internas. Por la diferencia de tiempo entre las señales enviadas y reflejadas, así como por la forma y amplitud de las señales reflejadas, se puede juzgar no sólo sobre el espesor del metal, sino también sobre los defectos encontrados a lo largo del camino de la señal ultrasónica. Un instrumento para realizar pruebas ultrasónicas no destructivas se llama detector de fallas. El detector de fallas utiliza transductores especiales (emisores – receptores de la señal ultrasónica) que permiten implementar los métodos de inspección tales como impulso de eco, espejo-eco y espejo-sombra.
Método de impulso de eco
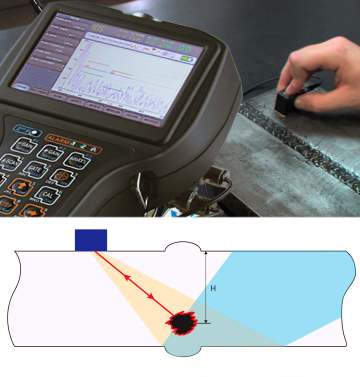
Con el método de impulso de eco, el transductor envía una señal de sondeo al objeto y recibe las señales de eco reflejadas por defectos y características de diseño del producto. El tiempo de su llegada permite determinar las coordenadas y la amplitud permite evaluar las dimensiones de los defectos.
La imperfección de este método es que la superficie reflectante del defecto debe ser perpendicular al haz ultrasónico, o el defecto está ubicado cerca de la superficie del producto. Por ejemplo, el método de impulso de eco no permite la detección de los defectos de superficie plana (grietas y faltas de fusión) que no se acercan a las superficies del producto.
Método de eco-espejo
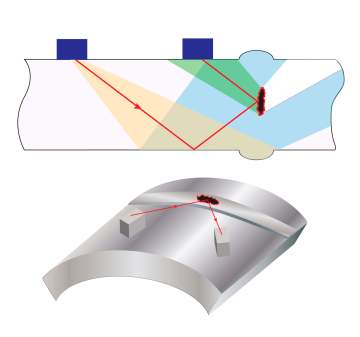
Por el contrario, los métodos de eco-espejo (Tandem y Duet) se utilizan para detectar los defectos de superficie plana (grietas y faltas de fusión). Estos métodos usan un par de transductores instalados de tal manera para que la señal emitida por el primer transductor regrese al segundo transductor después de la reflexión del defecto de superficie plana.
Método de espejo-sombra
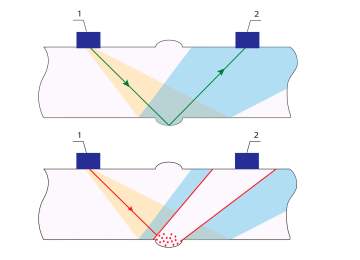
Sin embargo, incluso dicho método no garantiza la detección de defectos de todas las orientaciones. Para esto se usan el método de espejo-sombra. Cuando se realiza la inspección según este método, los sensores se instalan por ambos lados de la junta para que la señal reflejada de la superficie posterior caiga en el receptor. Los defectos bastante grandes de casi cualquier orientación que crucen el haz de ultrasonido sombrean la señal mencionada, lo que indica su detección. Pero este método, desafortunadamente, no proporciona información precisa sobre las coordenadas de los defectos detectados. Para obtener los valores precisos de un detector de fallas ultrasónico, es necesario configurarlo con antelación utilizando las muestras de ajuste especiales que se suministran con el detector de fallas.
Método TOFD
En las últimas décadas, el método de tiempo de difracción (TOFD) de inspección ultrasónica de las juntas soldadas se ha generalizado. El método TOFD se basa en la interacción de las ondas ultrasónicas con los bordes de las discontinuidades. Esta interacción conduce a la emisión de las ondas de difracción en una amplia gama de ángulos. La detección de las ondas de difracción permite establecer la presencia de discontinuidad. El tiempo de tránsito de las señales registradas es una medida de evaluación de la altura de la discontinuidad, permitiendo por lo mismo medir el defecto, y la dimensión de la discontinuidad siempre está determinada por el tiempo de paso de las señales de difracción.
La amplitud de la señal no se usa para determinar la dimensión. Además, se emiten y se aplican tanto las ondas longitudinales como transversales. La principal característica de información es el tiempo de llegada de la señal. El método TOFD tiene una serie de ventajas sobre los métodos convencionales de la inspección ultrasónica manual:
- Varias veces más productivo
- Baja sensibilidad a la orientación de los defectos
- Permite no evaluar, sino medir las verdaderas dimensiones de los defectos de superficie plana
- Alto grado de documentación de resultados de la inspección.
Para implementar el método TOFD, se usa un equipo especial que usa uno o más pares de transductores colocados a ambos lados de la junta y que se mueven a lo largo de la misma durante la inspección.
Inspección de corrientes Eddy
El ensayo no destructivo de corrientes Eddy se basa en el análisis de la interacción de un campo electromagnético externo con el campo electromagnético de las corrientes parásitas inducidas en el objeto de inspección por este campo. El principio de funcionamiento de los detectores de fallas de corrientes parásitas se basa en el método de corrientes parásitas, que consiste en la violación de las corrientes parásitas en la zona de inspección local y el registro de los cambios del campo electromagnético de las corrientes parásitas condicionadas por un defecto y por las propiedades electrofísicas del objeto de inspección. Se caracteriza por una pequeña profundidad de inspección. Se utiliza para detectar grietas y discontinuidades en el material a una profundidad de hasta 2 mm.
El diseño y los métodos de ajuste de los dispositivos de inspección de corrientes Eddy se parecen al diseño y métodos de ajuste de sus análogos ultrasónicos, en los mismos se utilizan los transductores de corrientes Eddy y las muestras estándar de corrientes Eddy, respectivamente. Es obvio que los métodos de inspección ultrasónica y de corrientes Eddy son mutuamente complementarios, asegurando la integridad y confiabilidad de la inspección de la junta soldada a lo largo de toda su profundidad y longitud. El equipo de ensayo no destructivo de corrientes Eddy de las juntas soldadas está fabricado por la sociedad “OKOndt GROUP” en forma de varios modelos de detectores de fallas.
Inspección por partículas magnéticas
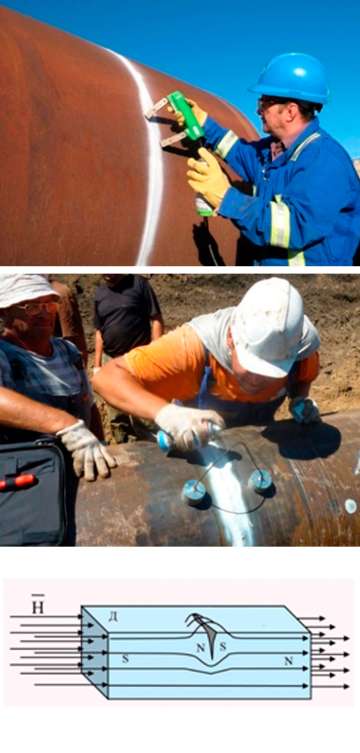
Inspección por partículas magnéticas o detección de defectos por partículas magnéticas es un método del ensayo no destructivo, basado en el fenómeno de atracción de partículas de un polvo magnético por flujos de dispersión magnéticos que surgen sobre los defectos en objetos de inspección magnetizados.
El método de inspección por partículas magnéticas está diseñado para detectar las violaciones de discontinuidad superficiales y subsuperficiales, tales como fisuras capilares, grietas de diversos orígenes, falta de fusión de las juntas soldadas, astillados, pliegues de laminado, desgarres, etc. El detector de fallas por partículas magnéticas permite controlar las piezas de diferentes formas, juntas soldadas, superficies internas de agujeros mediante la magnetización de áreas controladas individuales o del producto en general con un campo circular o longitudinal creado utilizando un juego de dispositivos de magnetización alimentados por la corriente de impulsos o continua, o utilizando imanes permanentes.
Inspección radiográfica
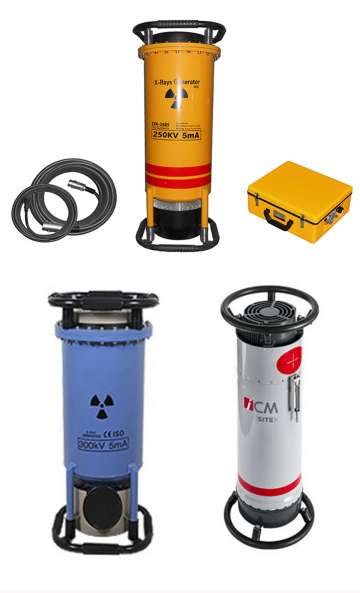
La información sobre la radiografía se proporciona en este artículo sólo para hacer que la situación de los métodos de ensayo no destructivo utilizado para controlar las juntas soldadas sea bastante completa. Aunque este método es muy preciso, su aplicación es bastante limitada, ya que está asociado con el uso de rayos gamma y rayos X con alto poder de penetración, lo que les permite pasar a través del metal, fijando defectos en la película. Esto condiciona su peligro elevado para la salud humana. Además, los instrumentos de este tipo son bastante caros. Por lo tanto, el uso de este tipo de inspección es muy específico y requiere el uso de los métodos de protección especiales y la creación de las condiciones de laboratorio apropiadas para la realización de la inspección. Por lo tanto, examinamos los métodos fundamentales del ensayo no destructivo de las juntas soldadas. Obviamente, que los resultados de inspección más precisos y las condiciones seguras de su implementación son proporcionados por el uso combinado de los métodos de inspección ultrasónica, de corrientes Eddy y por partículas magnéticas.